Introduction
Since its invention by Dr. Makoto Sagawa in Japan in 1982, NdFeB (neodymium-iron-boron) has emerged as the “Magnet King” in the field of permanent magnetic materials due to its ultra-high magnetic energy product and exceptional cost-effectiveness. It is widely used in smartphones, wind turbines, magnetic levitation trains, medical MRI equipment, and other fields, driving the progress of modern technology. This article will delve into its scientific properties, technical challenges, and future prospects.
I. The “Magnet King” Characteristics of NdFeB
Material Composition and Structure
NdFeB is composed of neodymium (Nd), iron (Fe), and boron (B), with its tetragonal crystal structure imparting high magnetocrystalline anisotropy, saturation magnetization, and structural stability.
Performance Parameters
Magnetic Energy Product: Can reach 400 kJ/m³, which is 10 times that of traditional ferrites.
Coercivity: As high as 2000 kA/m, with strong demagnetization resistance.
Operating Temperature: Regular grades have a temperature resistance of 80-200°C, which can be increased to 230°C with the addition of dysprosium (Dy).
II. Manufacturing Process
Powder Metallurgy Method
The mainstream process includes melting and rapid solidification, hydrogen decrepitation, magnetic field orientation and pressing, sintering, and tempering.
Bonded NdFeB Technology
Mixes magnetic powder with epoxy resin to create complex shapes, but with a 30% reduction in magnetic performance.
III. Application Fields
Green Energy
Wind turbines and electric vehicles utilize NdFeB to enhance efficiency and power density.
Consumer Electronics
Smartphone linear motors and wireless charging devices rely on NdFeB for precise haptic feedback and efficient charging.
Advanced Manufacturing
Magnetic levitation bearings and MRI equipment leverage NdFeB to increase rotational speed and imaging resolution.
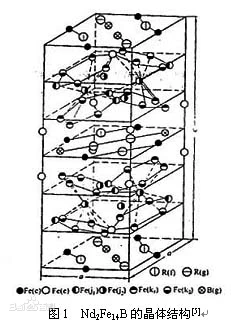
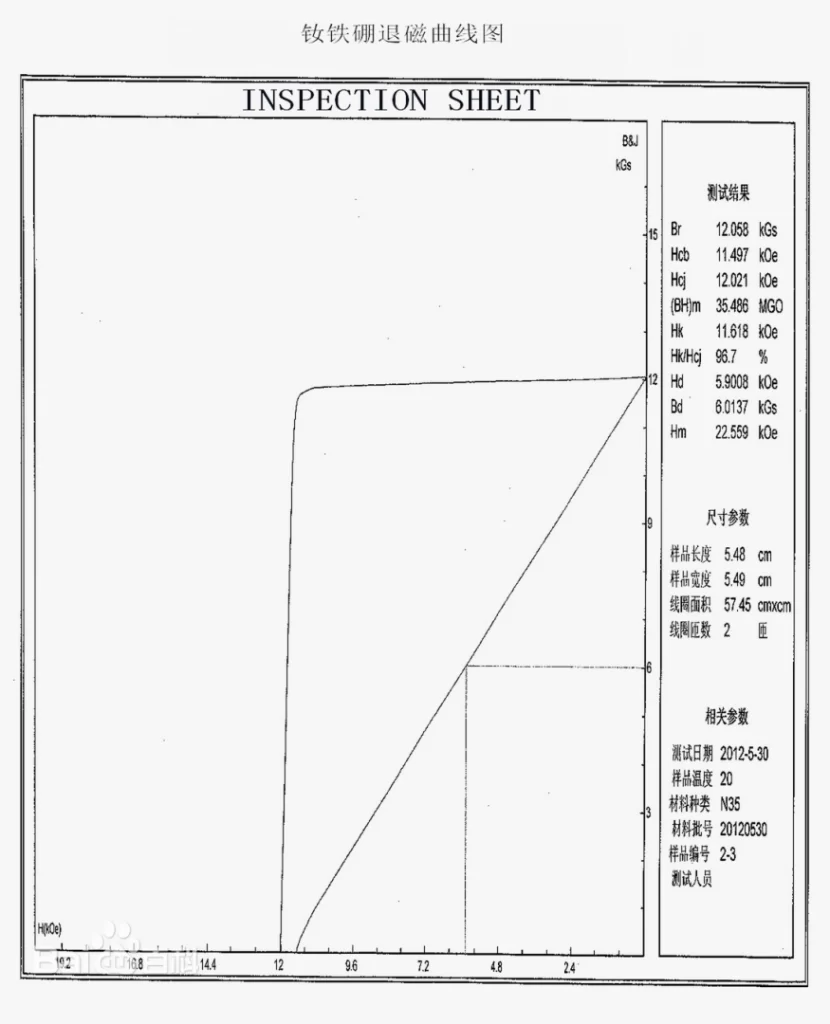
IV. Technical Challenges
Temperature Stability
NdFeB is prone to demagnetization at high temperatures, mitigated by grain boundary diffusion technology and dual-phase methods to enhance thermal stability.
Corrosion Resistance
Susceptible to oxidation, addressed through surface coating and encapsulation processes to improve corrosion resistance.
Rare Earth Resource Dependence
Depends on rare earth resources, reduced through grain boundary restructuring and recycling efforts to lower dysprosium content.
V. Future Directions
Ultra-High-Performance Materials
Aiming for a magnetic energy product exceeding 450 kJ/m³, utilizing nanocomposite magnets and hot deformation techniques.
Intelligence and Integration
Developing self-sensing magnets and 3D printing technology to enhance magnet intelligence and integration.
Sustainable Development
Developing rare earth-free magnets and biodegradable binders to reduce costs and environmental impact.
Conclusion
The rise of NdFeB has led a revolution in the industry. With the growth of sectors such as new energy vehicles and robotics, global demand for NdFeB will continue to increase. Overcoming resource constraints, innovating processes, and expanding applications will be key to future development. NdFeB is not only the “Magnet King” but also the “Universal Magnetic Link” in the smart society.