With the widespread application of sintered NdFeB materials in modern industrial and electronic technologies, particularly in fields such as new energy vehicles, industrial robots, and mobile intelligence, there is an increasing demand for NdFeB products to be lightweight, thin, miniaturized, and high-energy. This has led to increasingly stringent requirements for the magnetic energy product, coercivity, and thermal stability of these magnets. However, traditional manufacturing processes have faced a dilemma where enhancing the coercivity of sintered NdFeB often results in a decrease in remanence.
Doping the alloy with heavy rare earths such as Dy or Tb can increase the coercivity of the magnet, but this leads to a significant reduction in remanence due to the substantial incorporation of Dy and Tb into the main phase grains. Additionally, this process consumes large amounts of expensive heavy rare earth resources, significantly increasing the manufacturing cost of the magnets. The industry often uses BH_max (MGOe) + HcJ (kOe) to represent the comprehensive magnetic properties of a magnet. Therefore, how to further enhance the coercivity while maintaining high remanence, thereby producing magnets with high comprehensive magnetic properties, has become a research hotspot in the industry.
Grain boundary diffusion technology is a technique developed in recent years that can effectively improve the magnetic properties of sintered NdFeB magnets. By forming a layer of heavy rare earth film on the surface of the magnet steel and then undergoing vacuum heat treatment, the heavy rare earths can penetrate into the interior of the magnet along the grain boundaries. Simultaneously, the heavy rare earth atoms replace the Nd atoms surrounding the main phase grains to form a high-coercivity shell layer. This unique microstructure can significantly enhance the coercivity of the magnet with minimal reduction in remanence. Typically, for sintered NdFeB magnets with a thickness of less than 8mm, Dy-diffusion-induced HcJ enhancement can range from 4kOe to 7kOe, while Tb-diffusion-induced HcJ enhancement can range from 8kOe to 11kOe, with both diffusion processes resulting in a Br reduction of less than 0.3kGs.
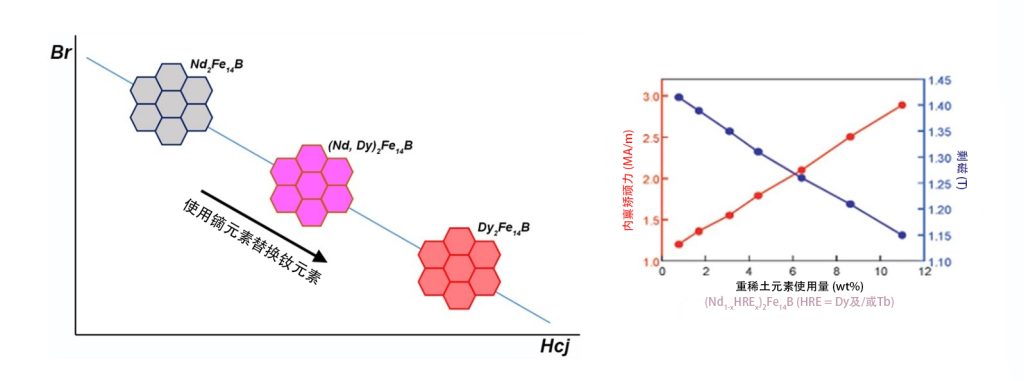
Compared to traditional non-diffusion magnets, the main advantages of grain boundary diffusion (GBD) technology are as follows:
- For same-grade magnets, GBD can significantly reduce the usage of Dy and Tb, resulting in lower costs.
- GBD enables the production of high-performance magnets, such as 50EH and 52UH, which are unattainable by traditional processes.
However, as with anything, GBD technology also has its limitations. For instance, due to the existence of a concentration gradient, the diffusion depth is limited. The thickness of mass-produced GBD magnets is typically within 10mm, which restricts the application scope of this technology.